Quizá te encuentres en el mismo punto que yo en tu viaje de reparación: sé cómo manejar un destornillador y un spudger, he reventado muchos cables y he cambiado mi ración de baterías hinchadas. Pero cada vez que me encontraba con conexiones soldadas, la espantosa retórica corporativa antirreparación se arremolinaba en mi mente: ¡Ponte en contacto con un técnico certificado!
Determinado a superar esta barrera, decidí tomar cartas en el asunto. Pedí consejo a colegas, vi vídeos instructivos, exploré foros e incluso me matriculé en una breve clase de iniciación para aumentar mi confianza y adquirir los conocimientos básicos para dar el paso. Para documentar mi viaje y enfrentarme a mis miedos, decidí compartir mis experiencias en este blog.
Aunque hay un puñado de disciplinas de soldadura, este artículo se centra en la soldadura simple de agujeros pasantes. Voy a repasar mi proceso mental para configurar mi estación de trabajo y, a continuación, pasaré directamente a un proyecto de soldadura de orificios pasantes.
Configurar mi estación de trabajo
Hay montones de artilugios y cachivaches para soldar en el mercado, pero me interesaba reunir lo básico para poder ponerme a soldar sin complicaciones. Pude equipar mi estación de trabajo con piezas y herramientas repartidas por la oficina, pero descubrí que podía comprar todo lo básico por unos 100 $, e incluso menos de 50 $ con compras de segunda mano y una pizca de creatividad. (También merece la pena que compruebes si tu biblioteca local de herramientas o tu espacio maker comunitario disponen de equipos de soldadura). Esta es la lista de las cosas que tengo en mi mesa de trabajo antes de entrar en más detalles:
- Estación de soldadura/puntas
- Soldador
- Limpiador de puntas (bola limpiadora o esponja)
- Fundente
- Mecha de soldadura
- Algo para sujetar tu proyecto
- Alicates de corte
- Mitigación de humos
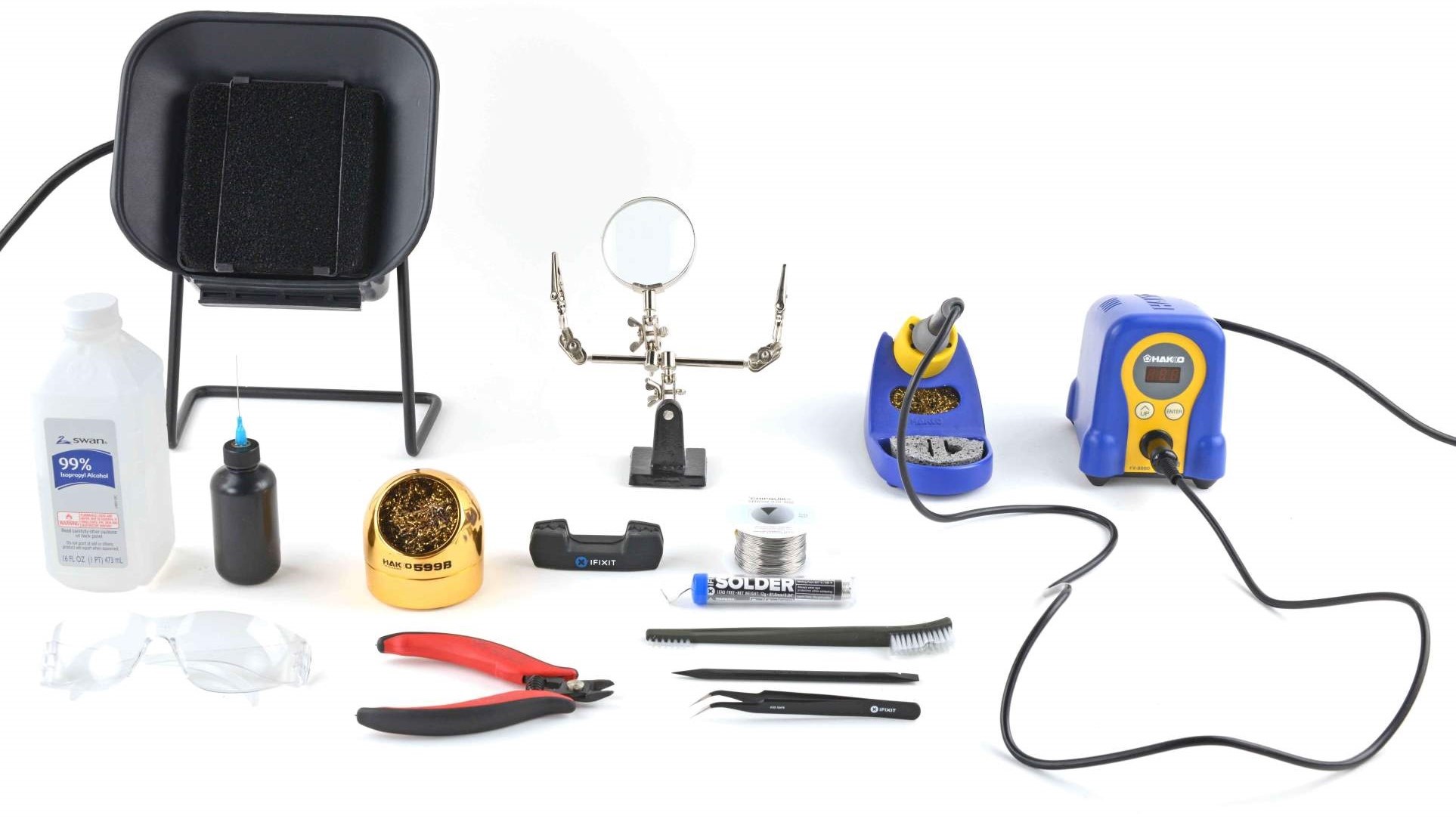
Estación de soldadura
El soldador es la varita mágica del alquimista electrónico moderno, que convierte el metal sólido en fundido.
Hay un montón de opciones «plug-and-play» económicas que funcionan en caso de apuro, pero yo me decantaría por una plancha de temperatura variable de al menos 60 vatios, sobre todo si piensas utilizar soldadura sin plomo, como es mi caso. Me ha resultado muy útil poder ajustar la temperatura sobre la marcha y confiar en que la plancha mantenga una temperatura constante. Estoy utilizando un Hakko FX888D, en parte porque es un soldador de eficacia probada, pero sobre todo porque lo tenía en el taller de la oficina..
Puntas de soldador
Un soldador sin punta es como un bolígrafo sin punta: todo el potencial, pero nada de punta.
Muchos soldadores se suministran con una punta cónica precisa, pero me pareció que la diminuta superficie de la punta tenía dificultades para mantener la temperatura ajustada. Me pareció que una punta de cincel más pequeña era más útil para soldar agujeros pasantes, al menos para las almohadillas relativamente grandes de mi proyecto. Estoy seguro de que encontraré más utilidades para las distintas puntas a medida que amplíe mi repertorio de soldaduras.
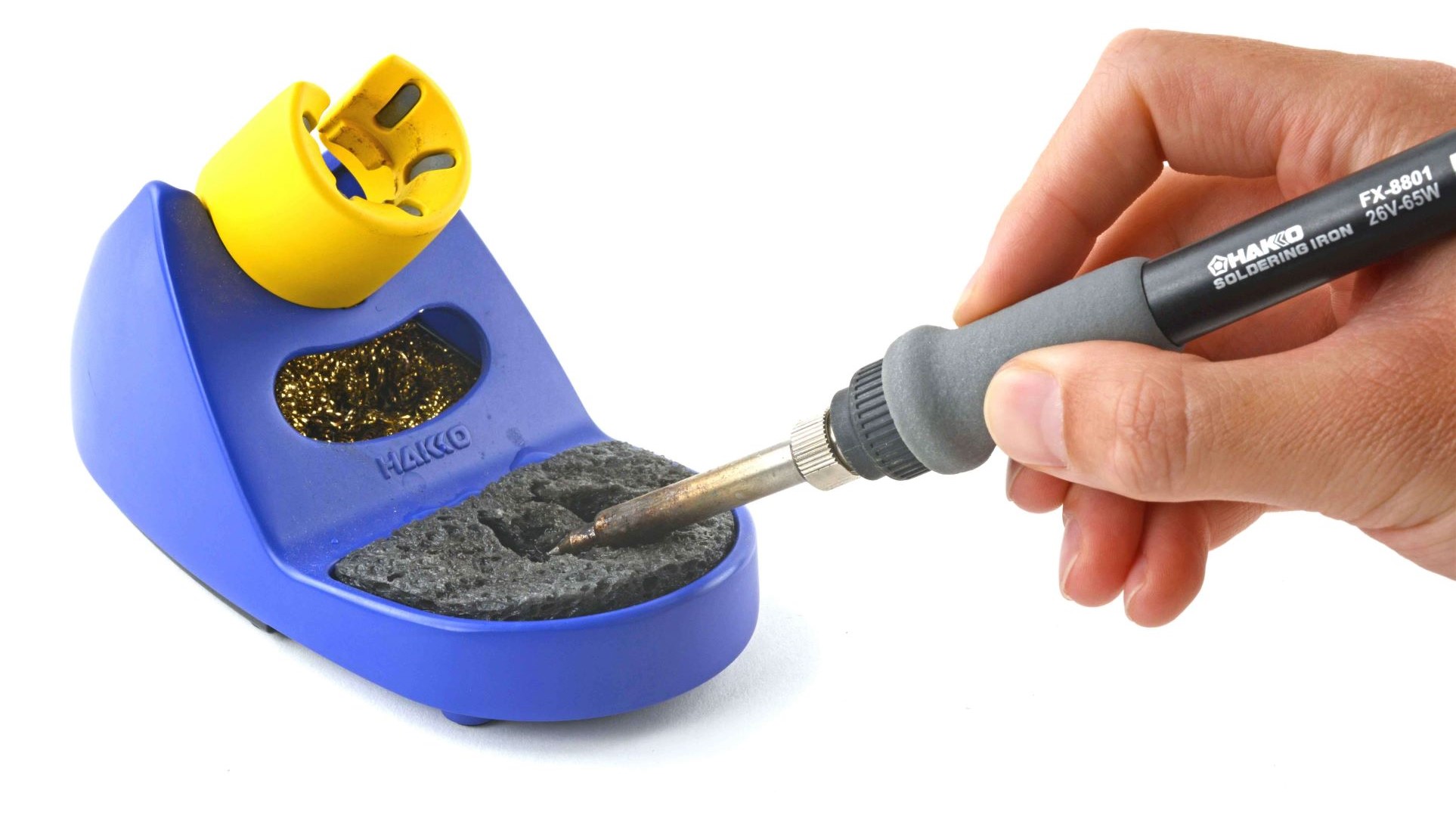
Limpiador de puntas
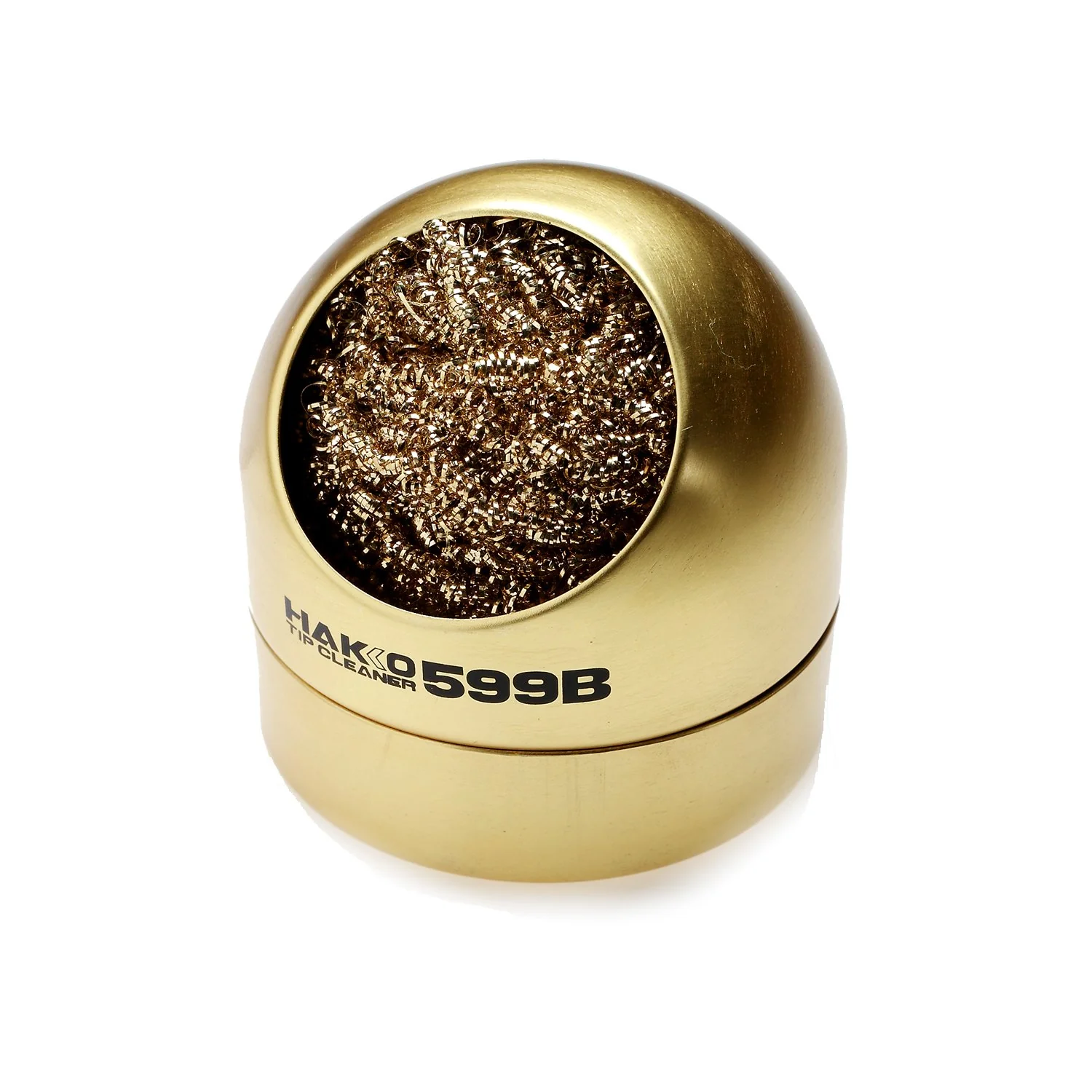
Las puntas de hierro son increíbles para conducir el calor, pero su conductividad se ve amenazada por la corrosión y la acumulación. El instructor de mi cartilla de soldadura mencionó que mantener la punta libre de suciedad y acumulaciones mejorará su conductividad térmica y prolongará su vida útil de forma espectacular. La mayoría de las estaciones de trabajo vienen con una pequeña esponja que puedes humedecer con agua destilada y limpiar la punta con ella, pero yo (y parece que la mayoría de los soldadores) prefiero las bolitas de bronce para limpiar limaduras por tres razones:
- No tienes que preocuparte de mantener la esponja húmeda.
- Las bolas de limpieza no reducen la temperatura de la punta.
- Su abrasividad tiende a limpiar la punta con mayor eficacia.
Soldadura
Aunque muchos aficionados prefieren la soldadura con plomo debido a su humectabilidad y a su punto de fusión más bajo, yo utilizo soldadura sin plomo. Aunque una plancha no debería calentarse lo suficiente como para liberar partículas de plomo en el aire, no me gusta nada la idea de manipular plomo: no es bueno para la salud. El plomo en los residuos electrónicos también es un enorme problema de seguridad para los recicladores y el medio ambiente.
Tras echar un vistazo a foros en los que se debatía sobre la soldadura con plomo frente a la soldadura sin plomo, me encontré con una cantidad desconcertante de odio hacia la soldadura sin plomo. Para ser sincero, mucho de eso me pareció una hipérbole. Con una plancha sólida y una preparación adecuada, trabajar con soldadura sin plomo es pan comido. Es definitivamente más cara, ¡pero una bobina decente me va a durar mucho tiempo!
Fundente
Aparte de un soldador y una plancha funcionales, mucha gente insiste en que el fundente es uno de los elementos más importantes de la caja de herramientas del soldador. El fundente es una solución ligeramente ácida que limpia los puntos de contacto, elimina la oxidación y ayuda a que la soldadura fluya. La mayoría de las soldaduras ya tienen un núcleo de fundente, pero yo siempre acababa necesitando un poco más.
Para soldar orificios pasantes, me aconsejaron que utilizara fundente a base de colofonia. La primera vez que soldé utilicé un bolígrafo de fundente, que me resultó muy cómodo y fácil de aplicar. Para este proyecto, sin embargo, acabé utilizando una jeringa de fundente sin limpieza con una punta precisa porque un generoso colega tenía un poco a mano. Para obtener más información sobre el fundente y decidir qué tipo es el mejor para cada caso, consulta este útil artículo.
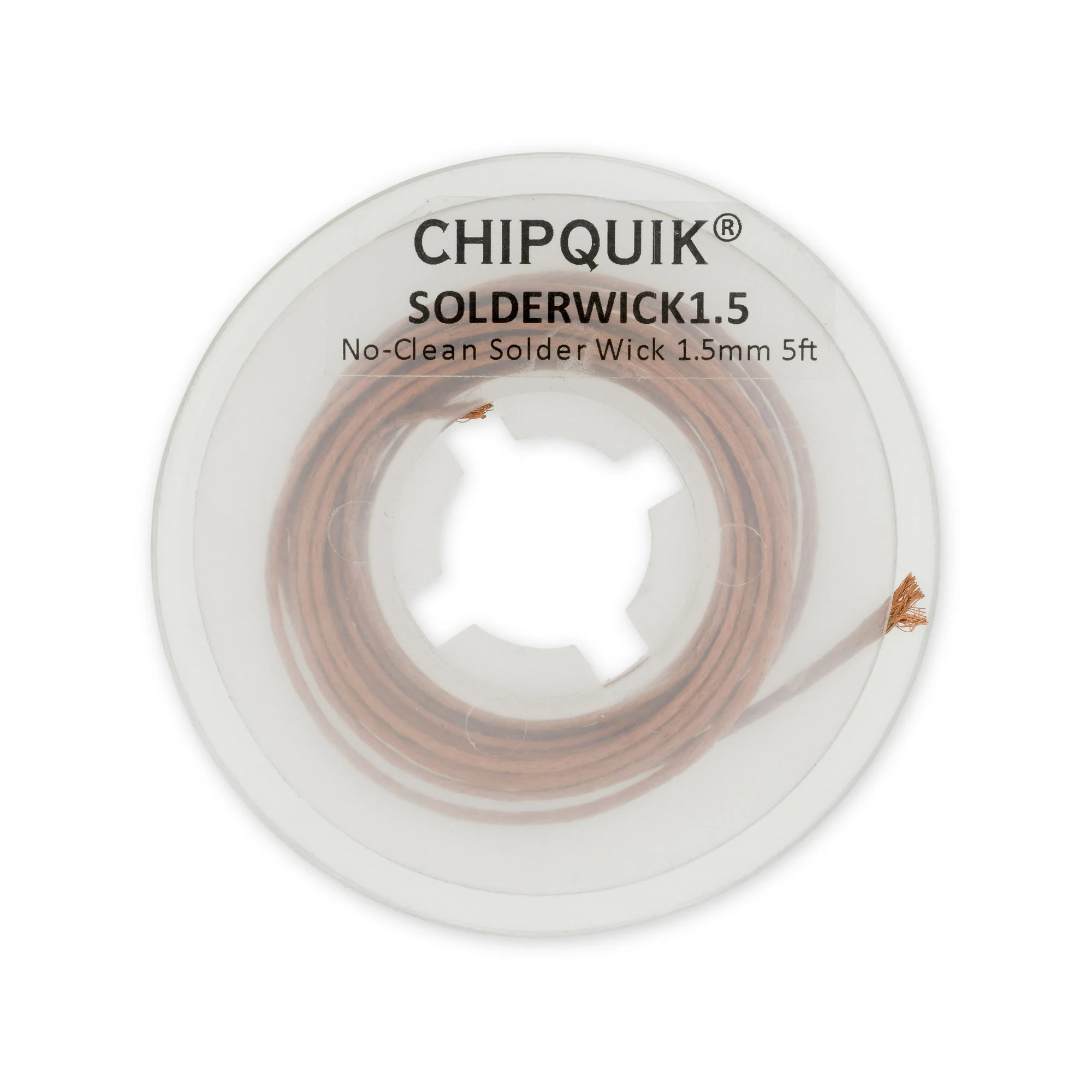
Mecha de soldar
Los accidentes ocurren, y aunque soldar parece indeleble, ¡desoldar es posible! Más adelante en este artículo cometí un error bastante grave al soldar (sigue leyendo para enterarte de todo), y descubrí que la mecha de soldar es una herramienta inestimable para limpiar mis errores. Intenté usar una bomba desolde, que aspira la soldadura fundida como una pajita, pero no tuve mucho éxito. Sin embargo, he visto algunos vídeos de gente que usa bombas desoldeadoras con excelentes resultados, así que sospecho que mi fracaso fue un problema de habilidad.
Alicate de corte al ras
Esto no entra en la categoría de estrictamente necesario, pero los alicates de corte al ras son útiles para recortar las patas que sobresalen de los componentes después de soldarlos en su lugar. En caso de apuro, apuesto a que la mayoría de los cortadores de alambre más pequeños harán el trabajo, siempre y cuando un poco de pierna extra que sobresale de la articulación no es un problema.
Algo para sujetar el proyecto
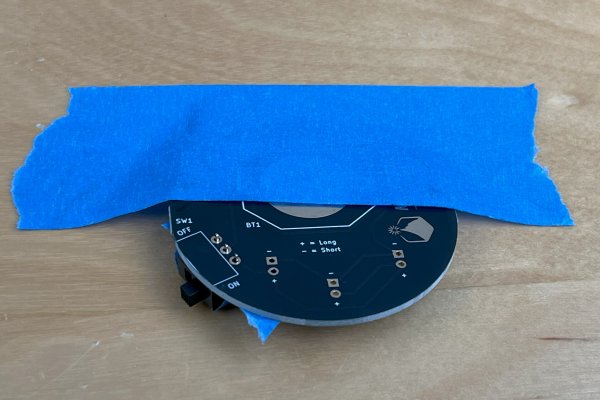
Algunos soldadores prefieren manos amigas o plantillas sofisticadas, pero yo utilicé una tira de cinta adhesiva para sujetar la placa en su sitio. Es muy barato y funciona muy bien.
Bien, ¡casi llegamos a la parte divertida! Una última nota muy importante.
Aburrido pero importante: ¡Seguridad!
A pesar de las ganas que tenía de ponerme manos a la obra, en mi cabeza resonaba un viejo adagio: La seguridad ante todo.
Para aventurar una conjetura, trabajar con metal fundido puede tener algunos peligros inherentes, así que hice un poco de tarea y compilé una breve lista de comprobación de seguridad. Estos son algunos de los principios de seguridad que me comprometí a seguir en mi puesto de trabajo:
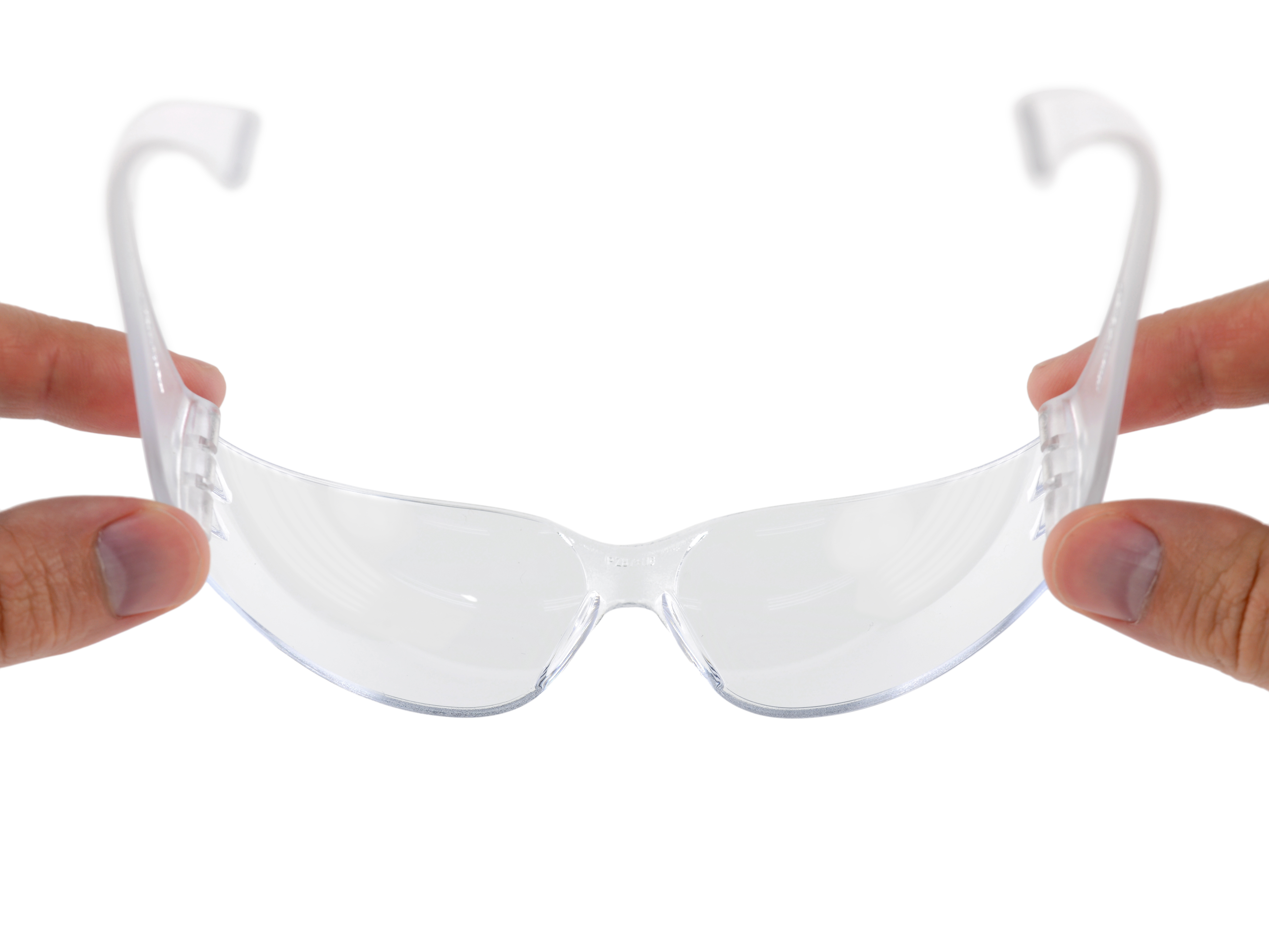
- Tengo el pelo largo, así que lo recogí y lo aparté del camino. Si tienes una barba de mago (no, no estoy celoso en absoluto, puedo dejarme crecer una) mantenla fuera de peligro.
- Aleja cualquier objeto inflamable. Aunque el éxito de un proyecto conlleva inevitablemente lágrimas de alegría, mantengo los pañuelos fuera del alcance de los niños cuando la plancha está caliente.
- Asegúrate de trabajar sobre superficies sólidas y resistentes al fuego. Yo tengo la suerte de contar con una mesa de madera maciza para trabajar, pero en mi lista de deseos figura un tapete de silicona para soldar encima.
- Metal fundido asegurando componentes=genial. Metal fundido en el ojo = ¡mi sueño infantil de ser pirata hecho realidad! Llevo gafas, que protegerán mis ojos. Ponte algo para protegerte los ojos.
- Siempre que no estoy soldando activamente, o si me levanto para ir al baño, apago el soldador. Es obvio que hay que evitar dejar el soldador desatendido.
Extracción de humos
Una buena regla general es no inhalar humo de ningún tipo, y eso es cierto cuando se trata de humos de soldadura. Al soldar, el humo visible es principalmente fundente vaporizado, que irrita los pulmones y puede causar todo tipo de dolencias desagradables con una exposición prolongada. En resumen, los humos de soldadura no deben llegar a los pulmones, así que tomo algunas precauciones para evitar inhalarlos.
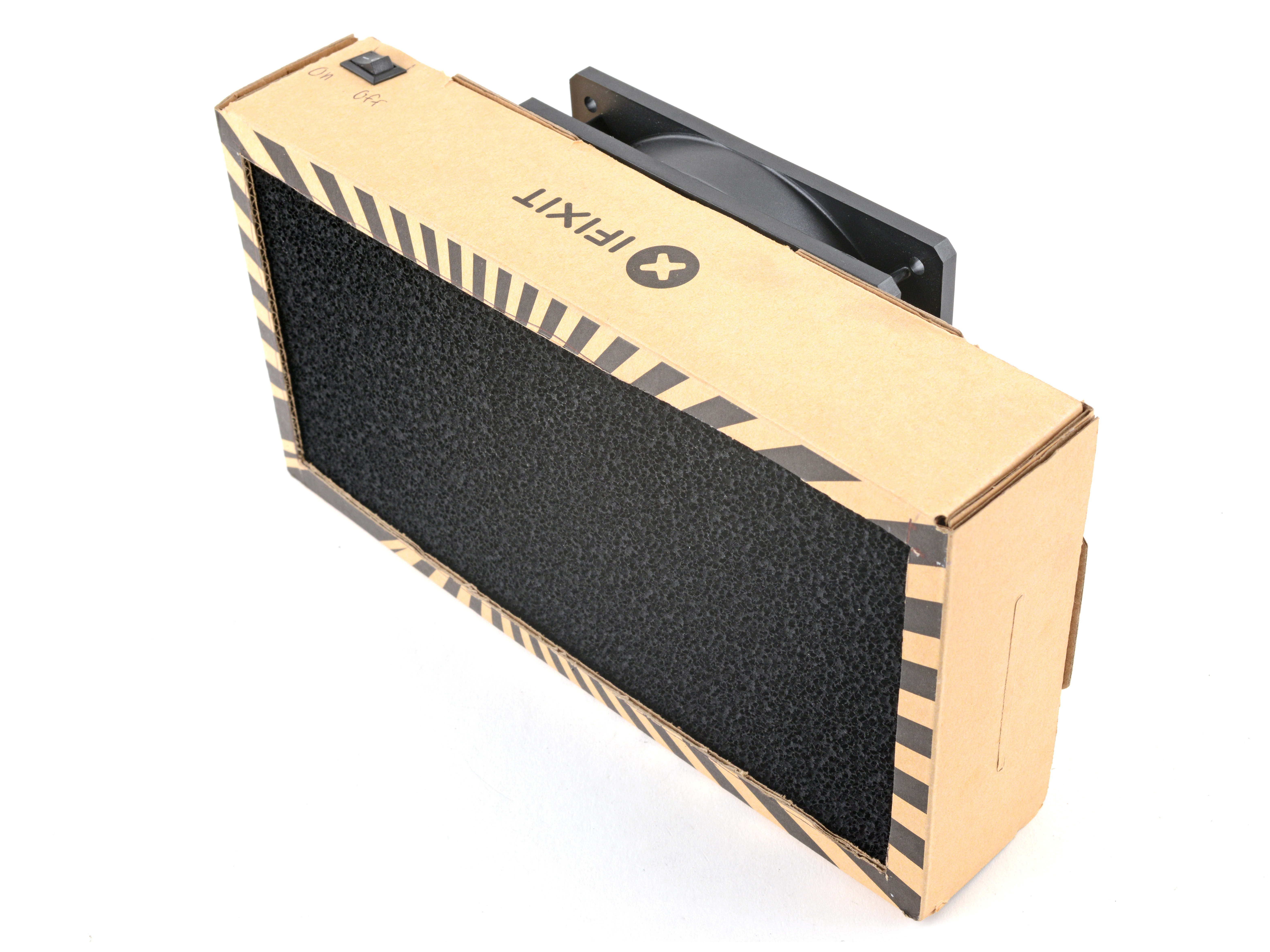
En el mercado existen muchos extractores de humos extremadamente caros y eficaces, pero son un poco exagerados para el aficionado medio como yo, que tiene unos índices de exposición relativamente bajos y no planea dedicarse profesionalmente a la soldadura.
Estoy utilizando un extractor de humo sencillo y relativamente barato que detendrá y dispersará parte de los humos. Una opción mucho más divertida y económica es construir el tuyo propio.
Sin embargo, como el medio filtrante del extractor que utilizo es carbón activado algo poroso, no confío en que elimine la mayoría de los humos/partículas, así que también ventilo mi espacio de trabajo. En el futuro, puede que instale un simple ventilador de ordenador conectado a un tubo que salga directamente al exterior (algo como esto) para evitar que los humos permanezcan en mi espacio de trabajo. Algunos me llamarán paranoico, pero la mitigación básica de los humos probablemente cueste menos que una simple visita al médico.
TL;DR: ¡Encuentra una forma de no inhalar humos de soldadura!
Por último, después de soldar, me lavo bien las manos, aunque utilice soldadura sin plomo. Esto es doble, triple y quizás cuádruple si acabo utilizando soldadura con plomo y/o trabajando con aparatos electrónicos antiguos; los aparatos electrónicos antiguos suelen contener montones de plomo. Aunque las soldaduras con plomo se han eliminado casi por completo en la electrónica de consumo moderna, voy a ir sobre seguro y asumir que cualquier placa que manipule contiene plomo.
Pongan en marcha sus motores
Ya tengo mi estación de trabajo preparada, las ventanas abiertas y el extractor de humos en marcha. Vamos a soldar. Espera… ¿qué estoy soldando otra vez?
Voy a empezar con un sencillo kit de agujeros pasantes, sólo para calentar mi plancha. La soldadura pasante consiste en insertar los cables de los componentes en orificios previamente taladrados en una placa de circuito impreso (PCB) y soldarlos en el lado opuesto.
Decidí empezar con un pequeño kit de agujeros pasantes por varias razones:
- Las instrucciones son sencillas y el tamaño de las almohadillas es bastante generoso.
- Sabré con relativa rapidez si he metido la pata o no. Sé que desmontar, desoldar, volver a soldar y volver a montar un proyecto más complejo sería aplastante sin un satisfactorio encendido al final del camino de las juntas de plata.
- Si te equivocas más allá del punto de no retorno, sólo pierdes lo que cuesta el kit, que generalmente no es mucho.
Estoy utilizando el Angry Storm Cloud de Alpenglow Industries, pero hay kits similares por todas partes. No hace gran cosa cuando está terminado, aparte de encender unos bonitos LED para mostrar que el circuito está completo y que las juntas son capaces de conducir una corriente.
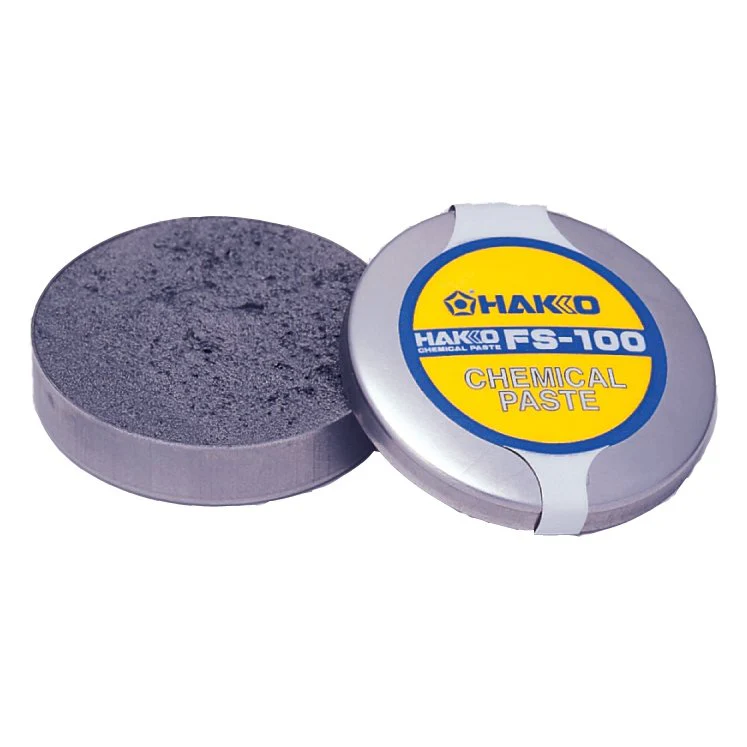
Calentar el soldador y estañar la punta
Un soldador frío es tan inútil como un palo de pogo en arenas movedizas, así que hay que calentarlo. La regla general para soldar sin plomo es alrededor de 400 °C. Yo estaba teniendo algunos problemas con la licuefacción de la soldadura a esa temperatura, así que lo subí a alrededor de 425 °C encontré mi soldadura mucho más dispuestos a ir con el flujo.
Después de calentar la plancha, limpié la punta con una bola de latón y la estañé. Estañar la punta es el proceso de recubrir la punta con una fina capa de soldadura, que ayuda a conservar la punta y a mejorar la conductividad térmica. Soldar es el nombre, pero la transferencia de calor es el juego.
Asegura el componente; ¡asegura la placa!
Con el soldador caliente y listo para la acción, decidí en una fracción de segundo que el primer componente que había que montar era el interruptor; por suerte, las instrucciones reflejaban mis instintos básicos. Introduje los cables por los orificios marcados, luego tomé una pequeña tira de cinta adhesiva y fijé el interruptor a ras de la placa. Luego le di la vuelta a la placa y lo pegué todo a la superficie de trabajo con los cables hacia arriba.
Aunque me encantaría echar un vistazo a otras plantillas del mercado, me di cuenta de que simplemente sujetar el proyecto con cinta adhesiva me permitía sujetar el soldador de forma natural, como si fuera un lápiz, con la mano apoyada en la superficie de trabajo para mayor estabilidad. La cinta adhesiva es ideal porque está diseñada para dejar un residuo mínimo.
Usa fundente
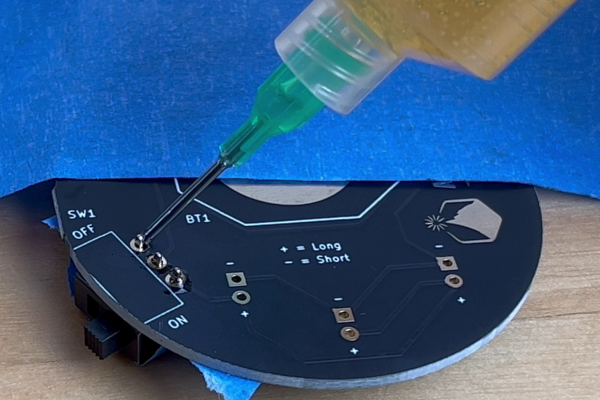
Antes de tomar el soldador, apliqué un poco de fundente en las almohadillas de cobre, y también un poco en los cables. Me he ensuciado un poco con el fundente, pero no pasa nada. Cuando termine de soldar, tomaré un paño sin pelusa humedecido con alcohol isopropílico de alta concentración y lo limpiaré. El fundente “sin limpieza” (un nombre inapropiado) que estoy usando es relativamente anticorrosivo, por lo que no es el fin del mundo si un poco de fundente acaba en la placa. Prefiero tener más fundente del que necesito que no tener suficiente.
Después de fundir un poco desordenadamente las almohadillas de cobre y los cables, llegó el momento de la verdad: ¿Tengo la entereza necesaria para colocar el metal?
Soldadura del interruptor
Con el interruptor fundido y asegurado, tomé el soldador caliente con la mano derecha y la bobina de soldadura con la izquierda. Toqué con la punta del soldador tanto el cable como la almohadilla de cobre, esperé un momento y luego introduje un poco de soldadura por el otro lado. Una nota rápida: asegúrate de tocar con el soldador tanto el cable como la almohadilla de cobre, o cualquier otra superficie que quieras unir. Esto es muy importante, ya que ambas superficies deben estar calientes para formar una conexión adecuada. Si las superficies no están bien calientes, crearás una conexión deficiente, o la soldadura se acumulará en el cable del componente en lugar de encapsularlo.
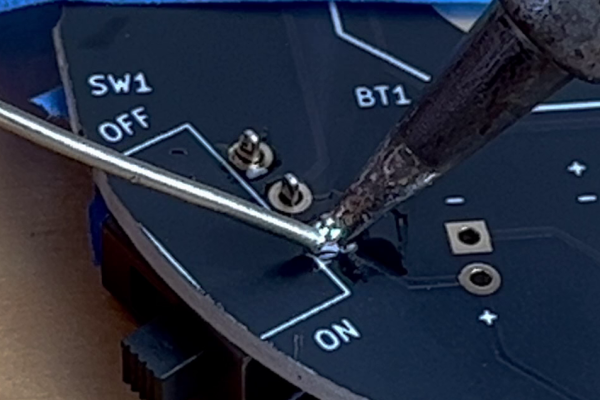
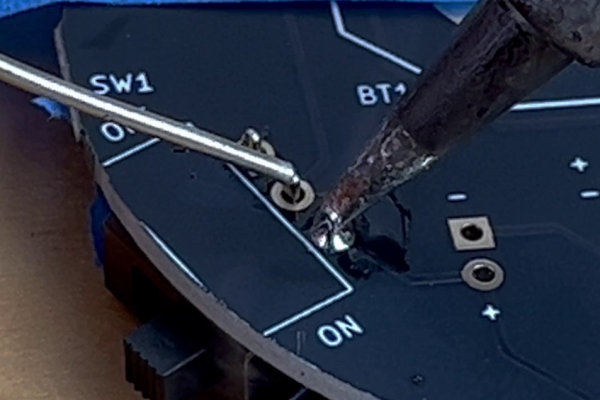
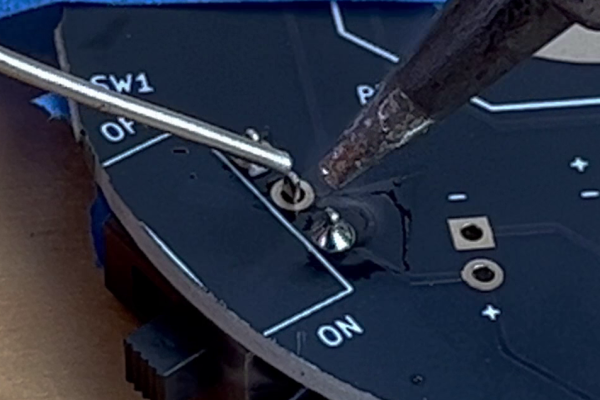
Después de que la soldadura se licuara y se acumulara alrededor de la junta, retiré el carrete de soldadura y dejé el soldador encendido un momento más para asegurarme de que la soldadura fluyera alrededor de toda la junta. Si retiras primero el soldador, también corres el riesgo de pegar todo el carrete de soldadura a la junta. Una vez que todo fluyó correctamente, retiré el soldador y ¡voilà! Se ha forjado una unión conductora. Antes de empezar con la siguiente conexión, pasé la punta del soldador por la bola de limpieza para mantener a raya la oxidación y las acumulaciones.
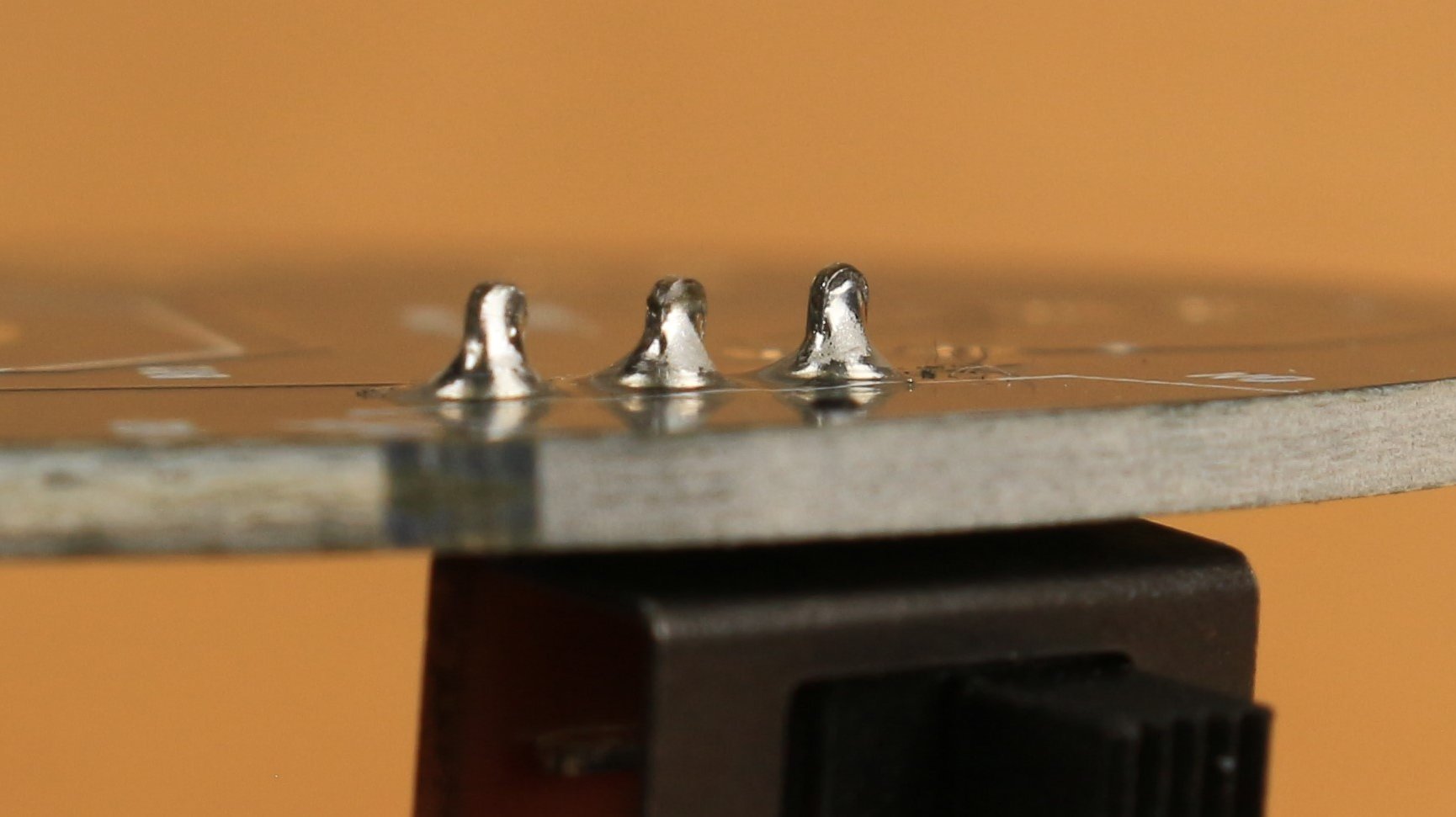
En general, ¡las conexiones tenían muy buen aspecto! Desde luego, no eran perfectas ni especialmente bonitas, ¡pero la visión de unas uniones (probablemente) conductoras me llenó de una oleada de satisfacción! En el futuro, puede que intente añadir un poco más de soldadura / soldar para crear una pendiente más suave y cóncava; ¡estoy pensando en un volcán de dibujos animados!
A continuación, los LED brillantes.
¡LEDs Entrantes!
Una vez asegurado el interruptor, los siguientes en unirse a la familia de circuitos son un conjunto de tres LED (diodos emisores de luz). Mientras que el interruptor tenía cables cortos y gruesos, los LED tienen dos patas largas y enjutas, una anódica (+) y otra catódica (-).
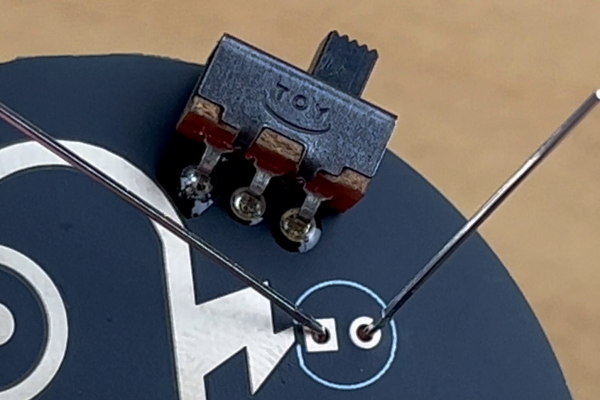
Introduje los LED a ras de la placa, con cuidado de asegurarme de que introducía los ánodos y los cátodos por los orificios correctos, y luego los doblé un poco para mantenerlos en su sitio. No dobles demasiado las patas, ya que dificultas que la soldadura fluya alrededor de toda la almohadilla.
Seguí el mismo procedimiento que con el interruptor y quedé bastante satisfecho con el aspecto de las juntas, aparte de que parecían un poco bulbosas. Cuando se trata de soldar, a veces menos es más.
Me adelanté y recorté las patas que sobresalían con un cúter. Se recomienda sujetar el cable mientras se corta para evitar que el metal salga volando por la habitación. Todos los presentes -y tu aspiradora- te lo agradecerán.
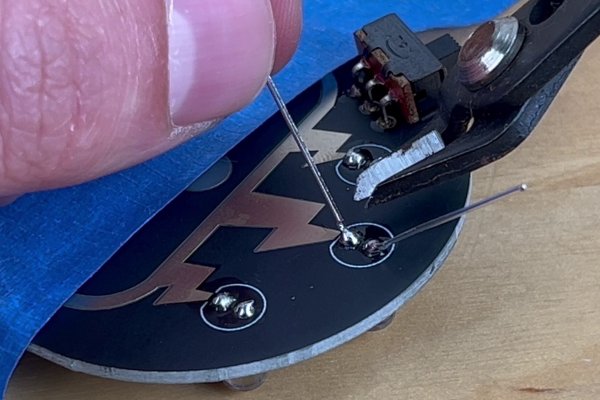
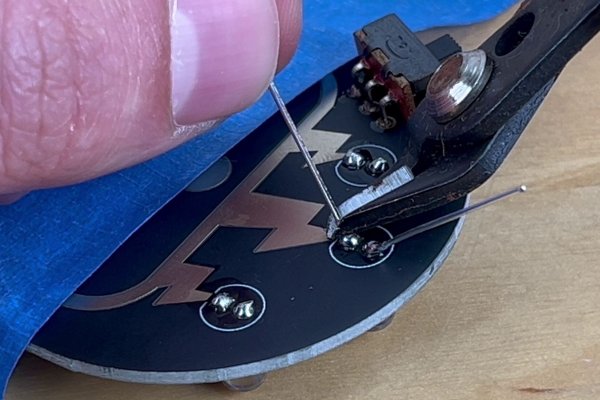
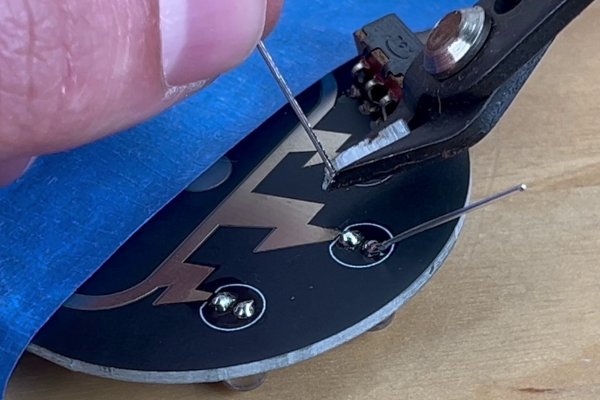
Pensé que estaba en buena forma, lista para pasar al componente final. Sin embargo, tras echar un vistazo a mi trabajo, me di cuenta de que había cometido un error monumental. Estaba concentrado en soldar, pero no tanto en asegurarme de insertar los LED por el lado correcto. En una vergonzosa pantalla de visión de túnel, transgredí el equivalente en soldadura del sagrado principio de “medir dos veces, cortar una”.
Técnicamente, podría haber seguido soldando y los LED se iluminarían perfectamente, aunque estuvieran orientados en la dirección equivocada. Pero ¡qué mejor momento para aprender a desoldar!
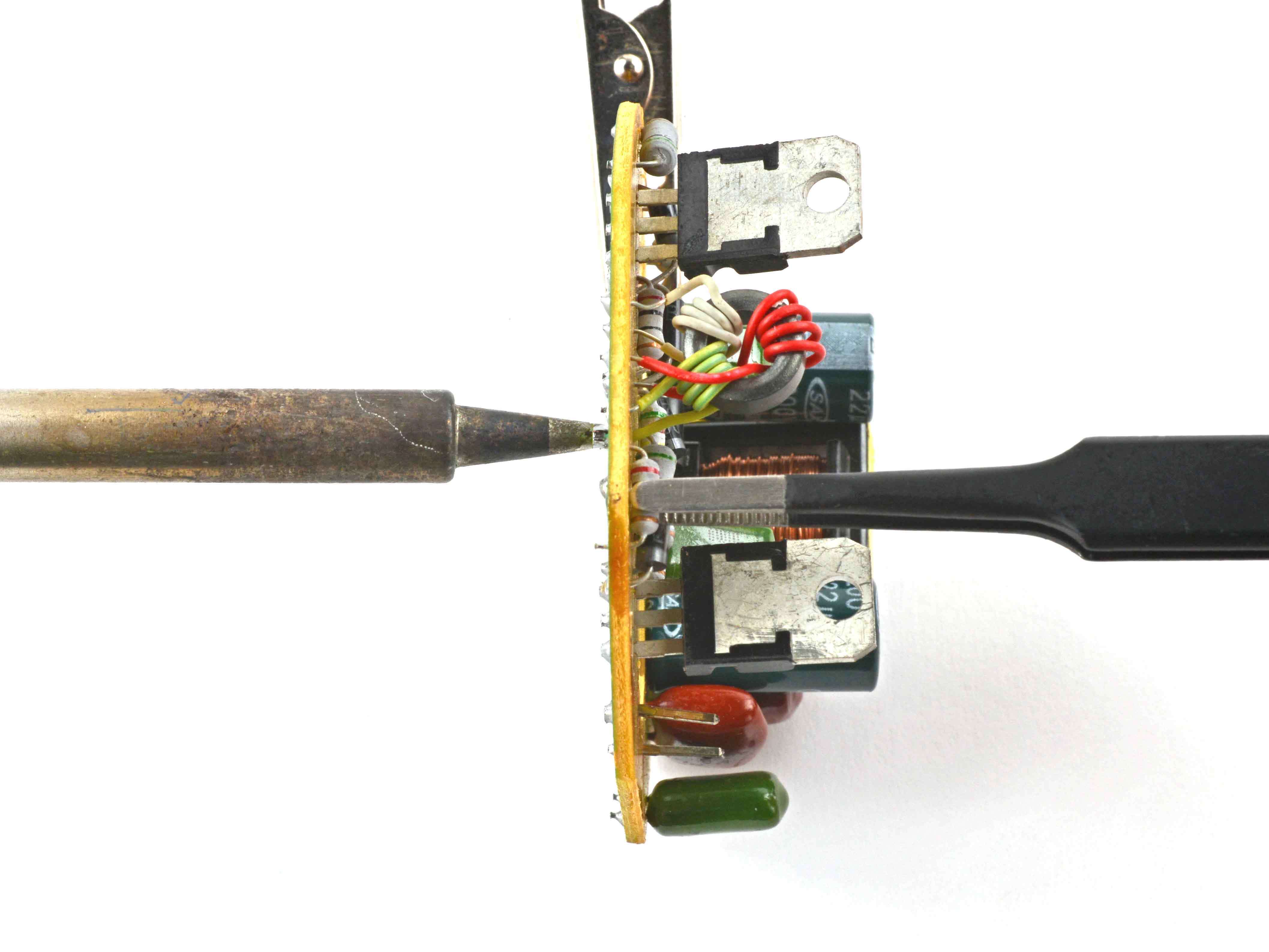
Desoldadura: Una demostración totalmente intencionada
Primero tomé un trozo de mecha de cobre y le puse un poco de fundente para ayudar a que la soldadura líquida penetrara en la mecha, como una pequeña esponja de cobre.
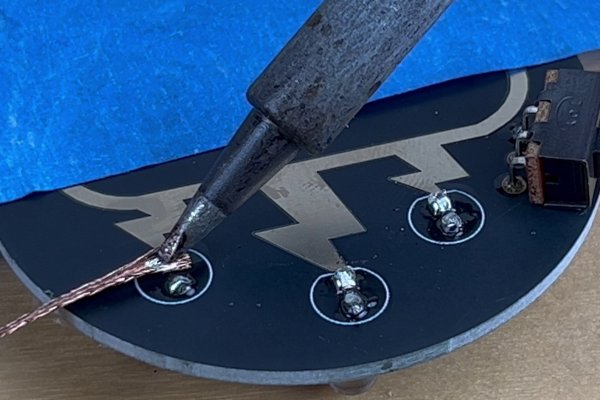
Con el soldador caliente, coloqué la mecha encima de la junta y, a continuación, ejercí una ligera presión hacia abajo con la punta del soldador. Me costó un poco eliminar la suficiente cantidad de soldadura para liberar los LED, pero cambiar el ángulo y recortar la mecha cuando se saturaba aceleró el proceso. Si tienes problemas, aplicar más flujo en la junta puede ayudar a que la soldadura fluya hacia la mecha. Cuando la mayor parte de la soldadura se introdujo en las hendiduras de cobre de la mecha, ¡los LED quedaron (casi) liberados!
Lo único que quedaba era enderezar los cables, ¡y luego simplemente los sacaba! Aunque desoldar es posible y necesario, te recomiendo encarecidamente que sueldes los componentes correctamente la primera vez.
Como ya había recortado las patas de los LED, tuve que pegarlos en su sitio antes de soldarlos en la orientación correcta. Con los LED orientados y asegurados en la dirección correcta, sólo queda el terminal de la batería. Una cinta adhesiva rápida, un par de puntos de soldadura en los “ojos” de la nube de tormenta, ¡y que se haga la luz! Antes de guardar el soldador, le di un buen repaso con la bola de limpieza y volví a estañar la punta.
Ahora, un momento de reflexión.
¿Cómo lo he hecho?
Echando un vistazo a las juntas, la calidad varía bastante. Los cables de los interruptores no son terribles, pero les falta un poco de soldadura y no se inclinan como me gustaría.
Las conexiones de los LED están un poco abotargadas y podrían hacer puente si añadiera un poco más de soldadura en algunos sitios.
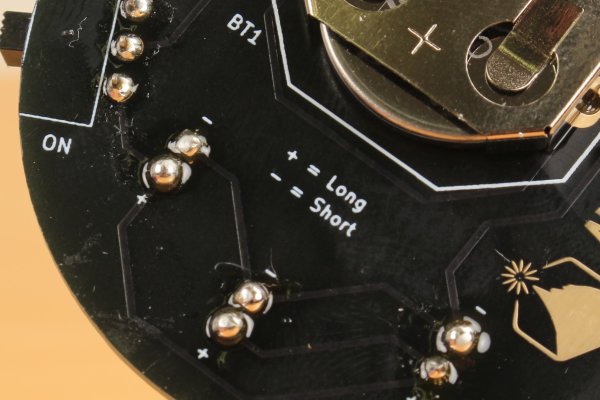
Mis juntas no son nada del otro mundo, pero he conseguido que los LED se iluminen y, por ahora, ¡eso me basta! Por no mencionar que tienen muchísimo mejor aspecto que mi primer proyecto, que te mostraré; quizá quieras respirar hondo y sentarte.
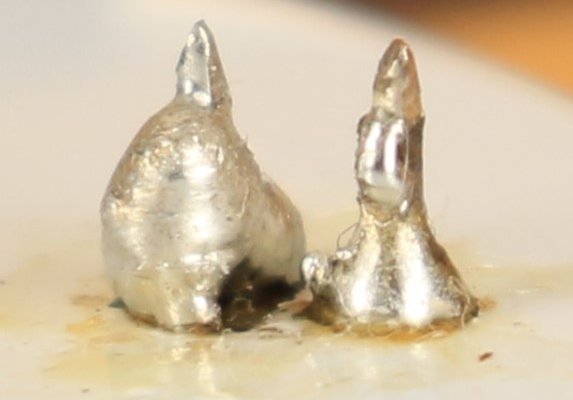
¡Caramba! En términos relativos, creo que esta vez lo he hecho bien, sobre todo si lo comparo con mi primer intento, aunque viendo esas articulaciones, quizá eso no sea decir mucho.
Reflexiones finales
Para mí, había una cierta mística en torno a la soldadura que se elevaba aún más con cada unión brillante: antes de empezar, soldar me parecía peligroso y prohibitivamente complejo. Es decir, no es peligroso, pero tampoco estamos trabajando con pólvora; y no es tan sencillo como girar un tornillo, pero tampoco es ciencia espacial. Bueno, algunas soldaduras son ciencia espacial, ¡pero eso no viene al caso!
La soldadura no está reservada sólo a los profesionales, y con el equipo adecuado y una actitud positiva, creo que cualquiera puede mejorar lo suficiente como para intensificar su juego de reparación y bricolaje y hacer realidad sus sueños de soldadura. Sí, mis conexiones no cumplen ninguna norma IPC, ¡pero los malditos LED se encienden!
Así que toma un soldador, respira hondo y sumérgete de lleno: te sorprenderá lo que puedes hacer con un poco de práctica y paciencia. Soldar es tanto para los profesionales como para el común de los mortales.
Artículo traducido por Mariana Roca.
0 Commenti